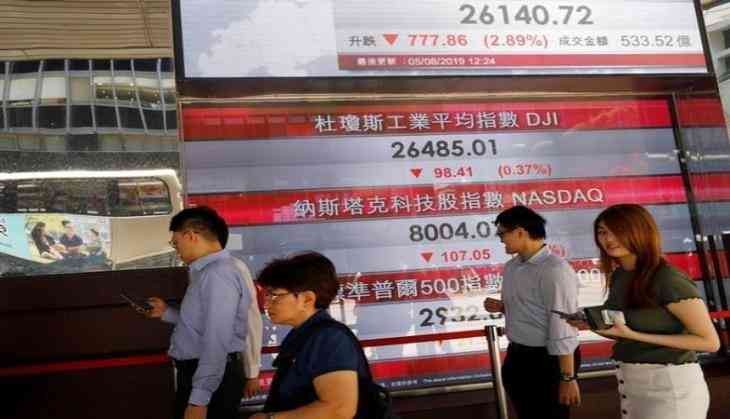
Out of 56 companies that relocated their production out of China between April 2018 and August 2019, only three went to India and two to Indonesia. This was the finding of a study by Nomura, a Japanese financial group.
Out of the 56 firms, 26 relocated to Vietnam, 11 went to Taiwan and eight to Thailand.
As the ongoing trade dispute between China and the US continues to escalate, tariffs are making exports from China more and more expensive for US importers. Many firms have been doing their sums and looking for new locations to re-site their manufacturing operations.
For many companies, the plan to relocate has already existed for a while. Costs in China were already trending up for some time. However, many hesitated because of the hassle and uncertainty of relocation. What tipped the scales in the last year or so was the additional US tariffs levied on Chinese made goods.
Re-locating manufacturing facilities is not a trivial matter. Besides, overcoming the high initial set-up costs, other factors to consider are infrastructure, communications and connectivity. Having good and cost-effective warehousing, transportation and other logistical support is essential. That is just the start. There is also the challenge of finding the right skilled manpower and thereafter putting the new workers through training specific to their production process. Further considerations include governmental support, a favourable tax regime and legal framework, and the ease and speed of starting a business in a new country.
On the surface, India and Indonesia both have the ideal demographics to be global manufacturing powerhouses to rival China which at the moment makes one-fifth of the world's goods. First of all, they have the second and fourth-largest populations in the world with India's population expected to surpass China's by 2030. They also have a relatively young population. United Nations estimates that India has a median age of 30, whereas Indonesia's median age is 31. By comparison, China's median age is 40.
Furthermore, India's labour cost is half that of China's.
So why are India and Indonesia not receiving their fair share of factories relocating from China?
Although both India and Indonesia's GDP growth rates are high compared with other major global economies, economists generally agree that they are both performing below their full potential with regards to FDI (Foreign Direct Investment) in manufacturing and hence they are both nicknamed "sleeping giants".
FDI is a good indication of external investor confidence in the success of economic reforms and prospects as they are a sign of how willing foreign corporations are willing to commit to long term investments in a country. FDI is necessary for a developing economy to create jobs, absorb excess labour supply and plug financial gaps. But India today pulls in a miserly 0.6 per cent of GDP in manufacturing FDI. Indonesia is a touch better at one per cent.
The most common reason touted by businesses about why they move to a particular location is the ease of doing business. In the Reuters story referred to earlier, a smartphone executive was quoting as saying that in Vietnam, there is a single point of contact, a person who takes care of everything from the government side.
Taking a leaf out of the book that Thailand and Vietnam use to attract FDI, both India and Indonesia need to further liberalise trade, spend more on infrastructure construction, reform land and labour laws and offer tax breaks for foreign investors. Legal reforms, liberation and favourable taxes are necessary for economies to reach their full potential.
The good news is that both countries are aware of this and making moves in the right direction.
In Indonesia, President Widodo is introducing tax incentive for foreign companies setting up manufacturing facilities in the country and making it easier for businesses to obtain a license.
The recent surprise cut in the corporate tax rate have appeased corporations and has helped put India in a new trajectory for growth. However, India needs to do more. For example, provide more tax incentives for investing in the desired type of manufacturing it hopes to attract - like high tech and electronics manufacturing for export. It must also make it easier to import components so that more of the assembly work can be done in India.
Infrastructure, as both countries are acutely aware, is also very important.
Indonesia announced they intend to spend 40 per cent of annual GDP on infrastructure over 5 years although financing it is an issue due to weak FDI inflows and limited room for manoeuvre in fiscal policy.
In both countries, there is a heavy dependence on-road transportation but if modern rail and water transportation are more readily available, it can save businesses significant costs and time.
The culture of manufacturing which is prevalent in countries like Germany, Japan, China and South Korea is missing in India and Indonesia. This means that not only must there be strong and readily available vocational training programmes to equip those interested with the necessary skills but that their smartest citizens must want to consider joining this sector.
Indonesia lacks graduates in degrees that support manufacturing. According to global business consulting firm McKinsey & Company, Indonesia only produces eight STEM (Science, Technology, Engineering and Mathematics) graduates per 1,000 citizens, while the figure is 20 for India and 34 for China.
What is heartening for India is that companies like Samsung and Apple are already making some of their mobile phones in India. Apple which has already been manufacturing iPhone components and older models in India expects to start building the newer iPhone XS and SR in India this year. The Samsung factory in Noida is one of its biggest in the world and 30 per cent of what it makes is exported.
Although there is progress, more has to be done if India aims to achieve PM Modi's aim, first declared in 2014, to increase manufacturing share of GDP to 25 per cent by 2025.
-ANI